Meet Hansel the alpaca.
He grazes in a Minnesota backyard. His coat is sheared annually and then is processed into yarn and knitted into a sweater so that you can bear chilly November.
The farm-to-consumer trend is moving beyond food to fashion, as more people want to trace a hat or mitten back to its origins. To meet the demand, fiber farmers, mill owners and artisans across Minnesota are banding together to produce ethically made, few-of-a-kind products.
Only a few mini fiber mills operate in Minnesota, producing products from alpacas, llamas and sheep. They're supplied by a few dozen farmers who raise alpacas in Minnesota, according to the Alpaca Owners Association. Wool comes from about 2,000 American farms.
Rachel Boucher owns a fiber farm and custom processing mill in Hastings, where Hansel lives. She offers tours of her ranch and meet-and-greets with the alpacas, sheep, llamas and goats that she's been raising for more than 10 years. This month, she opened a store on her property to sell yarn and bundles of cushy fiber called roving.
Meeting her animals, like Larry the lamb, pleases her customers, Boucher said. "They've seen the sheep, they know he's healthy and hasn't been mistreated."
For years, journalists have probed the poor conditions in factories where low-paid workers make mass-produced clothing. An investigation of the online retailer ASOS by BuzzFeed News and several other news outlets reported recently that workers were unable to take bathroom or water breaks or had assignments canceled after they became sick at work. The 2013 collapse of a garment factory in Bangladesh — where 1,100 people died — prompted protests of hazardous working conditions across that country.
People increasingly want to know the lineage of their threads — just like their meat or produce. And they're willing to pay more for the good stuff. "In order to pay my employees a living wage," Boucher said, "it's going to be $20 a skein."
"People are asking questions," said Jess Daniels, a Minneapolis project manager for Fibershed, a California nonprofit founded in 2010. What was once "Who made my clothes?" has become "Who grew my clothes?" Daniels said.
Artisans and farmers showcase and sell their products at fiber festivals and farmers markets. And the internet is weaving more opportunity for collaboration and commerce. A study published in August by Helen Trejo, a researcher in fiber and apparel design at Cornell University, found that social media has become a new marketplace for buyers who want to see and read about the emotional connections between the animals and their owners.
"If you can source your product back to the very animal, people get all excited about that," said Teresa Kukowski, owner of Hollyhock Farm Alpacas in Becker, who sends her fiber to be processed at Boucher's farm. "They find it entertaining at the very least."
The processing mill in Hastings employs four employees who clean, sort and spin fiber from animals across the Upper Midwest on decades-old machines.
It's a promoter of "slow fashion," a term that was coined in 2007 by fashion consultant Kate Fletcher, according to Trejo.
Some proponents of the movement are trying to have one outfit made a year from locally sourced natural fibers.
"You can't automate this. You can't just throw [fiber] into a machine and have it come out the other end," Boucher said — "unless you're working with synthetics."
Natalie Daher • 612-673-1775
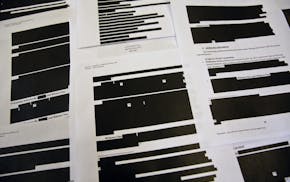
Want to share info with the Star Tribune? How to do it securely
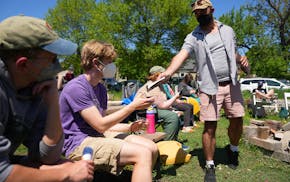
'Safe recovery sites' would offer syringes, naloxone and more to people using drugs. The plan could be in peril.
New Minnesota GOP leaders seek peace with party's anti-establishment wing
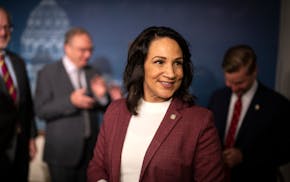
Who is Republican Lisa Demuth, Minnesota's first House speaker of color?
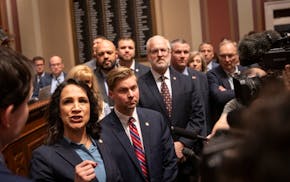