The white trailer blends into the winter landscape at SKB Environmental's landfill in Rosemount, but inside, machinery is working to capture one of the most pervasive environmental pollutants of our time.
The landfill is the final stop for industrial waste, incinerator ash and demolition garbage, where all of that material is mixed into massive, lined cells. Like in every landfill, moisture in the trash that's trucked in mixes with rainfall and collects into a polluted soup known as leachate.
SKB is experimenting with filtering PFAS chemicals out of that liquid. The leachate is pumped inside the trailer, where it travels through several tanks that repeatedly froth it up. These chemicals bubble into a super-concentrated foam – much like soap. Then that foam is siphoned off, and the cleaned water continues to a sewage plant.
PFAS, or per- and polyfluoroalkyl substances, are thousands of chemicals used to make everything from nonstick frying pans to stain-resistant clothing and carpets; it's even used to snuff out dangerous fires. The chemicals' almost unbreakable carbon-fluorine bonds make them useful, but also ensure they don't break down. They have been found to persist in the environment across the globe, including in the bodies of people and animals.
Growing research shows that these chemicals are toxic, linked to some cancers and reproductive, developmental and immune system issues.
In the past few years, regulation of these chemicals is finally starting to catch up to the danger – the EPA set new limits for six PFAS in drinking water last year, and private startups are racing to find a way to destroy them. But decades' worth of the compounds are sitting in landfills right now – presenting a contaminant to manage for waste handlers who didn't create the pollution, but now find themselves awash in it.
Researchers are still trying to understand whether the chemicals are also escaping into the air, via gasses from landfills, aeration in wastewater treatment and the emissions from incinerators, said Detlef Knappe, a professor of environmental engineering at North Carolina State University.
A few waste companies are trying to get ahead of the curve. Ryan O'Gara, government affairs manager at SKB, said the company is expecting a future where new regulations would force the waste industry to reckon with the PFAS flowing through it.
"We might as well be on the leading edge of it, as opposed to trying to catch up later," O'Gara said.
At the company's Rosemount landfill, early tests are showing some promising results. Tests of the filtered leachate show that the process is capturing nearly all of two of the oldest – and most toxic – forms of these chemicals, said James Locurto, a project manager with the landfill's contractor, Sanexen Altra.
Eventually, Locurto's company hopes to treat 72,000 gallons of leachate a day.
Stopping the source
It's little surprise that PFAS are ending up in our waste. For years, the chemicals have been used in food containers, clothing, carpeting, cookware, cosmetics and even some medicines, all of which can end up in garbage cans.
There's hope that a wide-ranging PFAS ban that Minnesota passed last year, the strictest so far, will help lessen the burden. By 2032, almost everything sold in the state will have to be free of the chemicals. Some of the most common products that use PFAS must comply as early as 2025, including makeup, clothing, home textiles and cookware.
The federal government is also making slow strides – the Food and Drug Administration announced Feb. 28 that PFAS had been voluntarily phased out of U.S. paper and cardboard food packaging.
In Minnesota, the waste industry has supported these moves, hoping it would reduce its own burden.
In historic cases where waste operations haven't been properly managed, the costs have been severe.
The Minnesota Pollution Control Agency has found that 100 closed landfills are leaking some amount of the chemicals – and in the worst case, groundwater contamination was 1,000 times worse than the state's limit.
For the most part, drinking water has not been affected, but MPCA does provide bottled water to three families whose well water has been contaminated by PFOA from landfills, an agency spokesman said.
Tested technology
In Rosemount, SKB plans to test not only its filtering system – known as foam fractionation – but also several technologies that claim to either lock up or destroy PFAS. In one case, it will try to use concentrated PFAS liquid to cure concrete that would go back into the landfill.
The science of PFAS destruction is still developing, in a technological race that could spur a lucrative industry.
But in another part of the state, waste handlers are relying on older technology.
In St. Louis County in northern Minnesota, where Dave Fink manages environmental services for the rural areas outside of Duluth, the options seemed stark. The county landfill serves a large, rural section of Minnesota's biggest county. It's one of eight counties across the state that spray their treated landfill leachate directly onto fields.
That leachate filters directly into groundwater, and faces some of the strictest state pollution rules, Fink said. But none of them addressed PFAS, and sending the liquid to a sewage plant in nearby Duluth would do little, ultimately depositing the chemicals into Lake Superior.
"We wanted to do our part to keep [our] fraction of the wastewater out of Lake Superior," Fink said. "And we knew we could."
Knappe, the environmental engineering professor, said that in many cases, landfill leachate has a higher concentration of PFAS than wastewater, but the higher volume of effluent coming out of a sewage plant usually makes it a more consequential source of the chemicals for the environment.
In general, the wastewater industry says it's too expensive and not technologically possible to filter all their material for PFAS. Minnesota estimated last year that it would cost between $14 billion and $28 billion over two decades to filter out all the PFAS that flow to sewage plants.
Building the future
Instead of relying on a sewage plant, St. Louis County is building its own facility, on a much smaller scale. It will use two older technologies – granular activated carbon and reverse osmosis – to filter the PFAS out of leachate, and then take the concentrated liquid that remains and put it back in the landfill.
The hope is to create a closed loop for the chemicals, and keep them contained, rather than spraying them onto a field or letting them flow into Lake Superior. If new methods to destroy or trap PFAS end up working, there will be room in the new building to install them, Fink said.
Knappe said that for the smaller volume of liquids that landfills produce, this loop might work for now. But a few of the new destruction technologies that use high pressure in their process "have really strong potential to succeed," based on some early published research.
St. Louis County's new treatment plant will cost between $15 million and $17 million, with a combination of state, county and federal American Rescue Plan funds. That's part of the reason why St. Louis County is using well-worn filtration methods – the federal dollars require the plant to be running by 2026, so the technology needs to be ready.
The hope, Fink said, is that the investment will serve the waste system for years, even beyond PFAS. "We're hoping to capture the next contaminants of concern that come down the pike," he said.
This story is a product of the Mississippi River Basin Ag & Water Desk, an independent reporting network based at the University of Missouri in partnership with Report for America, with major funding from the Walton Family Foundation. Sign up to republish stories like this one for free.
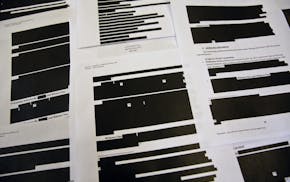
Want to share info with the Star Tribune? How to do it securely
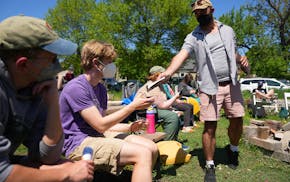
'Safe recovery sites' would offer syringes, naloxone and more to people using drugs. The plan could be in peril.
New Minnesota GOP leaders seek peace with party's anti-establishment wing
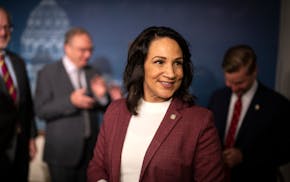
Who is Republican Lisa Demuth, Minnesota's first House speaker of color?
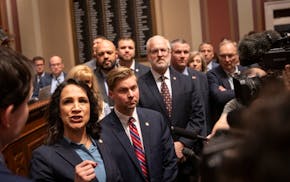