It's a familiar sight in Midwestern homes: a plastic bag full of plastic bags.
For the first time, those bags can be recycled locally and put to good use by preventing plastic waste in landfills, lakes and streets.
A $30 million plastic recycling facility opened in Rogers in August that aims to make a dent in the global glut of single-use plastic waste. Myplas USA takes in films, wraps, bags and other items that are hard to recycle and turns out tons of tiny plastic pellets other manufacturers can use as part of new products.
Even before all four recycling lines at the Rogers facility have opened — that's expected by 2025 — the CEO of the South African company sees an opportunity to expand.
"I can easily see a universe where we create a mega-site in Minnesota," Andrew Pieterse said in an interview. "At the same time we're looking at where we grow elsewhere in the Midwest," which could include more sites in the North Star State.
Unlike rigid plastic, flexible plastic films are not typically handled by traditional recyclers (and still should not be placed in curbside bins since they can get caught in machinery). Myplas has found a cost-effective process to handle only flexible plastic, in part by ensuring there is a supply of plastic to recycle and demand for the recycled pellets.
Myplas has partnered with several major Minnesota businesses to ensure a steady stream of plastic comes in. That includes shrink wrap used on pallets of General Mills products, boat wraps, protective films — and plastic shopping bags that consumers drop off at Target stores.
The recycler has also partnered with manufacturers and end users.
The business collective MBold championed the project and helped get a $13 million investment for Myplas from General Mills, Schwan's, Charter Next Generation, Target and Ecolab.
Environmental groups argue that ending fossil fuel-based plastic use should take priority over recycling it. But without affordable and readily available alternatives, consumers and companies continue to choose the convenience of plastic bags and films and send billions of pounds of it to landfills — and the ocean — every year. Just 5% of this type of plastic is recycled annually.
Preventing even a small fraction of that waste, as the tons of plastic in a Rogers warehouse represent, is what drives Pieterse and has helped him quickly hire a staff of 50.
"This is not just a job. This is meaningful, this is what we all need to be doing in some way, shape or form," he said. "Because if you want to get really philosophical, our planet is dying. So what we're doing here is trying to slow that down."
A view from the floor
Earlier this week, enormous bales of plastic bags and films were stacked in one corner of a 170,000-square-foot warehouse in a sprawling industrial park on the east edge of the Twin Cities suburb.
The blocks of plastic were destined for sorting, which is partly a mechanical process but largely a manual one. After a machine separates pieces of plastic from bales, a line of employees manually inspects and separates different types of plastic, sending some down the conveyor line and other pieces to the floor to be gathered and sorted once more.
This is part of why plastic film recycling has been slow to take off. The different types of plastics used in flexible films can't be combined for their second life — and manually sorting them is a costly endeavor.
After sorting comes cleaning, melting, extruding and pelletizing through a variety of connected, and gleamingly new, equipment.
In January, the towering machines should be humming 24/7, or close to it, when a third shift is fully staffed, Pieterse said. And two more recycling lines still need to be installed to reach full capacity of about 90 million pounds annually in early 2025.
That's about 20% of the plastic Minnesota consumes every year, based on national plastic use of about 12 billion to 15 billion pounds.
Pieterse said the company's experience in South Africa, where Myplas was founded in 2012, gives it a head-start over competitors.
"It takes skill to operate a recycling plant. It's not just flicking a switch and getting pellets," he said. "Our first batch was absolute rubbish. But our eighth was on spec, which was brilliant. That was pretty impressive."
Local solution, global problem
Myplas was first to announce a plastic film recycling plant in the Midwest early in 2022, but other companies have followed suit in Indiana and Ohio.
"Which is great," Pieterse said. "It's a huge problem we want to solve."
The United Nations sees plastic waste as a growing threat to the environment, especially marine environments, and to human health.
"The level of greenhouse gas emissions associated with the production, use and disposal of conventional fossil fuel-based plastics is forecast to grow to 19% of the global carbon budget by 2040," a U.N. Environment Program report found.
Food companies in particular have come to rely on plastic lining and film to ship food farther and keep it on shelves longer, reducing food scarcity in the process.
Incorporating more recycled plastic is one part of a broader set of solutions to replace the single-use plastics that have come to dominate and define many aspects of modern life in just the past 50 years.
"A single-solution strategy will be inadequate to reduce the amount of plastics entering the oceans," the U.N. report says. Circular-economy policies, regulations, incentives, taxes and initiatives to change consumer attitudes toward plastic are just some of the ways plastic pollution can be tackled.
The Myplas plant is seen as part of that "circularity" solution, by keeping plastics in use longer.
"This new facility really is the culmination of collaboration and problem solving to bring this circular economy into reality," said JoAnne Berkenkamp, managing director of MBold. "It's really important to bring these flexible films to grocery stores and other locations that have take-back programs."
Pieterse says that adding more Myplas factories around the region will help make a meaningful difference in how much plastic is reused and how much continues to pollute the planet.
"The beauty of the design of the plant is it is highly scalable and replicable in a short space of time," he said. "And that's kind of our growth strategy."
Party City to shutter hundreds of stores across the U.S., including 10 in Minnesota
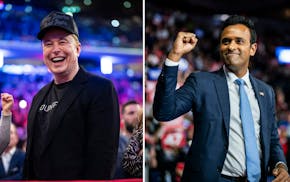
Ramstad: Let's create more modest expectations about reining in federal spending
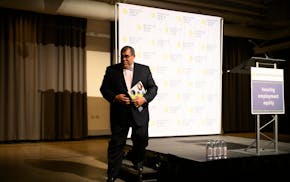
St. Paul civic booster Paul Williams looks back, and forward, as he retires from Project for Pride in Living
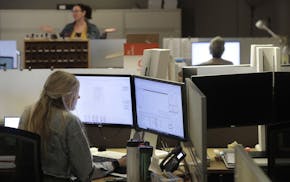
Yuen: What do women want from the workplace in 2025?
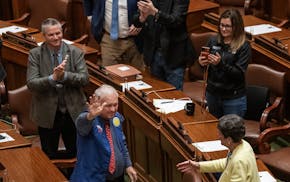