Business at warehouses around Minnesota and the U.S. has ramped up recently, a sign both companies and consumers are scrambling to stock up on imported goods amid President Donald Trump's trade war.
Starting in February, Trump has imposed tariffs on Minnesota's biggest trading partners: Canada, Mexico and China. Imports from China incur tariffs of up to 145%, prompting the Asian country to respond with its own retaliatory tariffs. Other countries, including Canada and Mexico, face a blanket tariff of 10%, with potential increases paused for 90 days until July.
Manufacturers "seem to have ramped up production to build inventory and secure supply chains" in anticipation of tariff-related price increases, according to location analytics platform Placer.ai, which uses foot traffic data collected from mobile devices to generate metrics tracking how many people visit a business. Its data showed visits to industrial manufacturing facilities in Minnesota increased by about 4% in March since the previous month.
A U.S. Commerce Department report released Wednesday reinforced that finding, saying the country's gross domestic product dropped by 0.3% in the first quarter of 2025. Economists attributed that to companies and consumers creating a surge of imports by stocking up before the full force of tariffs hit, which decreases U.S. economic output.
A stockpiling surge might offer short-term stability, but "it also raises concerns about how manufacturers will manage longer-term cost pressures and supply chain challenges if tariffs are enacted," said the recent Placer.ai report.
Twin Cities industrial real estate was already in high demand before tariffs triggered the import wave. Increasing rates of online shopping at e-tailers like Amazon, which often ships products in two days or less, made warehouse space across the country a necessity.
That left the industrial sector as one of the few bright spots in commercial real estate, which has struggled as demand for office space tanked amid post-pandemic remote and hybrid work.
In the first quarter of 2025, the Twin Cities had one of the lowest vacancy rates for industrial buildings in the country at 4.2%, according to analysts at Colliers, a Minneapolis-based commercial real estate agency.
Construction on big projects like industrial warehouses or apartment buildings has come nearly to a halt as developers wrestle with high construction costs and stingy lenders. So demand is unlikely to ease if supply isn't increasing.
Manufacturers are anticipating tariffs will drive up their costs, forcing American companies that depend on imports to pass that on to consumers via higher prices. Higher prices could, in turn, reduce consumer demand for their wares.
Unsure what will happen in the next few months, companies have put off acting on longer-term expansion, said Rob Kress, CEO of Waypost Advisors, a supply chain consulting firm for manufacturers and distribution companies.
Opus, one of the Twin Cities' largest commercial real estate developers, just completed its Dayton Parkway Business Center, an industrial property of more than 130,000 square feet. The building opened in March with its first tenant TurbinePROs — which installs, maintains and repairs rotating equipment — occupying about two-thirds of the building.
Although companies have expressed interest in the remaining space, said Joe Mahoney, Opus' senior director of real estate development, it hasn't yet leased.
Nate Erickson is a senior vice president at Transwestern, a Houston-based real-estate company with a regional office in Minneapolis. He said companies' sizes influence their tariff responses.
"Some of the larger companies might be pushing to stockpile more inventory," he said, "but some of the smaller companies that have less of an ability to do that, they're really struggling."
Larger companies have the facilities to stock up on raw materials or finished goods "and can ride out the volatility," Erickson said. But smaller companies "are really sweating bullets."
"'This is really challenging,'" Erickson said small businesses are saying, "'and we don't know if we're going to make it.'"
Even Fortune 500 companies have their reservations about stocking up in hopes of avoiding higher tariffs. Minneapolis-based retailer Target hurried to acquire merchandise when panic-buying led to empty shelves early on in the pandemic. But that backfired, leaving Target with expensive and bulky backlogs of furniture and home electronics. The company had to slash prices and cancel vendor orders among other steps to unload inventory.
Erickson said instances like that have left company leaders wary "they're going to be stuck with this stuff."
Uncertainty persists for Minnesota farmers, businesses as courts toggle tariffs
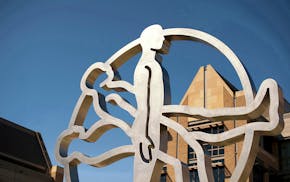
Medtronic ups return-to-office policy for hybrid workers to four days a week
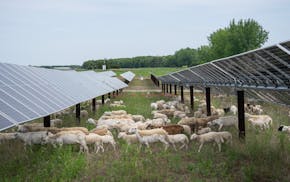
Xcel lets loose a small army of hungry sheep to keep its solar farm in order
![Frozen Jennie-O turkeys photographed at a Cub Foods store in St. Paul, Minn., on Monday, November 15, 2021. ] Elizabeth Flores • liz.flores@startri](https://arc.stimg.co/startribunemedia/U74OMTK3OMVA7SBJ2BTZ5SF4D4.jpg?h=91&w=145&fit=crop&bg=999&crop=faces)
Hormel's Jennie-O turkey sales surge as competitors contract
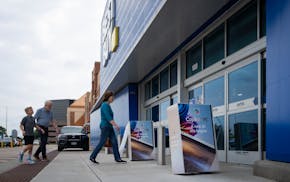